Austin Anderson is currently a Graduate Intern in Objects Conservation at the Walters Art Museum, Baltimore, and presented on his research into fabricating missing elements for an ornate ormolu wall sconce.
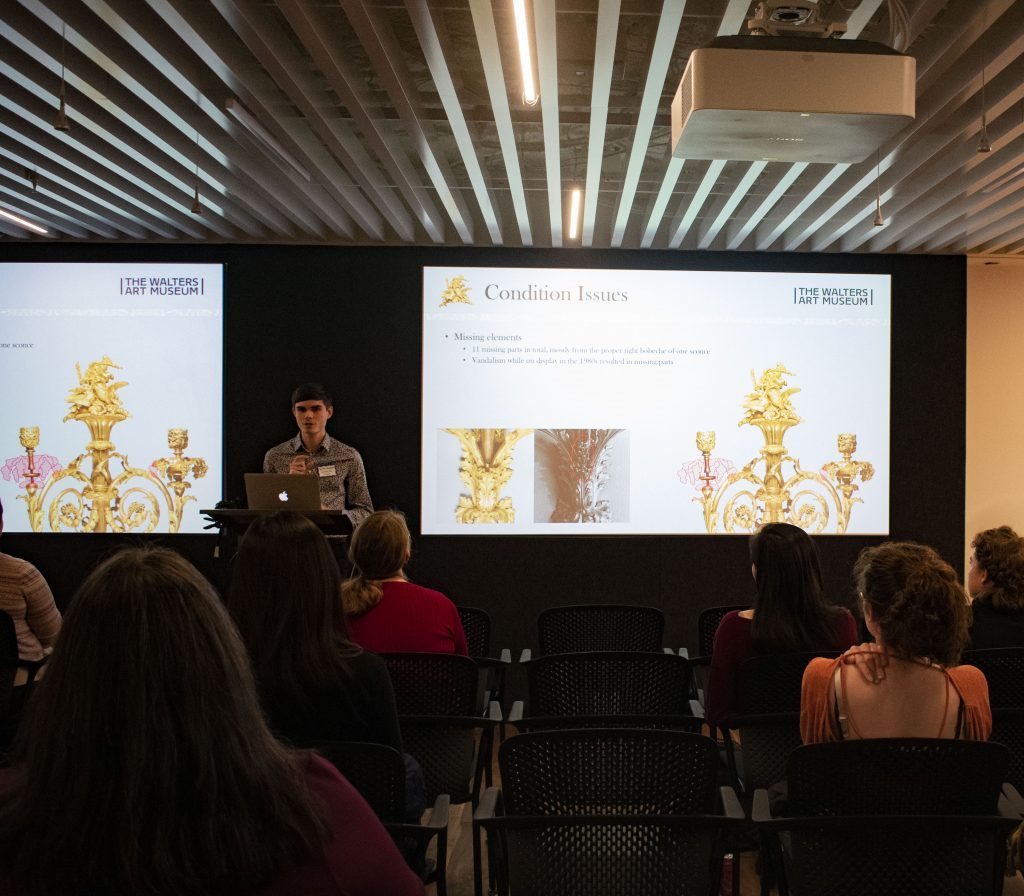
The sconce had been constructed in the 18th century by a father-son pair. It was a complex design with over 35 parts, screws, nails, tensions rods, and so on, and was made of gilt brass. Austin explained the process of gilding involved mixing the gold with mercury and brushing it on forming an overall matt surface that was then burnished shiny in areas for effect.
The sconce was missing 11 parts, but strangely in photographic records it seemed complete. A chance conversation with the previous director of conservation solved the mystery. Whilst on display in the 1980s staff kept finding golden pieces hidden around the museum, eventually realizing they had been stolen from the sconce and perhaps stashed to be retrieved later.
Aside from the missing pieces, the sconce had some corrosion – identified as copper sulphide and copper carbonate corrosion products, was overall dirty and grimy, and had previous soldered restorations.
Through discussion with the curator, the goal for the treatment was to replicate 9 of the parts which were visible in the archival photographs in order to make the sconce more legible for visitors. Luckily, these parts were mirrored elsewhere on the sconce and could be directly copied.
The big question for Austin’s research was the best way to replicate the varying matt-shiny surface of the original mercury-gilding. Methods such as 3-D printing or electroforming could be possible, but he focused on molding and casting. First, he created a mold with a silicone putty over a bunch of grapes which had a barrier coating of Paraloid B-72. Materials and methods tested then rejected include:
- Terracotta MilliputTM, painted with GoldenTM acrylic iridescent paints, then coated with Regalrez 1094.
- Dusting the mold with mica powder, then filling with a mixture of terracotta and white Milliput® and bronze dust. The overall appearance was improved, but he was concerned the bronze powder would tarnish over time.
- Dusting the mold with bronze powder, then filling it with plaster. The powder poorly adhered to the surface and the overall piece was too fragile for the necessary structural attachment to the sconce.
- Dusting the mold, then filling it with Hxtal NYL-1 bulked with bronze powder. The extended curing caused the bronze powder to settle over time, and it required a very high ratio of powder.
- Coating the surface of the casting with a gold leaf pen (Krylon 18K Gold). However, the piece was too detailed for an even surface finish, even when the solution was removed from the applicator and applied with different brushes.
The best result came from:
- A 2-part silicone rubber mold (Smooth-On Oomoo 25); and,
- Casting a Hxtal epoxy resin, then coating the surface with GoldenTM acrylic iridescent paint, followed by dark washes of Acrysol WS-24 to highlight the texture and gold leaf on raised areas for the original burnished details.
Summarized by Karen Wilcox