On March 23, metalsmith Michael Brehl expertly guided us through the production of a silver ring, helping us to understand the working properties of the metal, the marks made by various tools, and some of the differences between the artifacts of manufacture and the artifacts of use and damage.
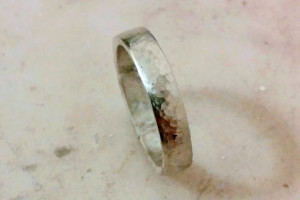
We began by cutting up pieces of silver to re-use and placed them in Michael’s small electric forge. While the silver was melting down, we had an extensive discussion about fire scale on metal objects. The conservators in the room had many questions that led to a lengthy discussion on this subject. We also discussed the difference between chasing and repoussé, and had a chance to try out the tools used for these techniques.
When the silver was ready, Michael poured the ingots out himself while we watched; pouring ingots is tricky, he said, and everyone spills some the first time. The silver was a red-hot liquid at this point so I was happy not to have to risk spilling it on my shoes. When the metal cooled, the ingots were dropped in an acidic pickle bath to remove oxidation from the surface.
The rest of the process we did ourselves. Once the ingots were poured, we put them through a rolling mill with graduated-sized grooves to create long, thin rectangular pieces. This left some flashing that we had to file off before beginning to shape the pieces into the style of our choice. Some participants began pulling the ingots through progressively smaller draw plates to make wire, which they then twisted. Others put their ingots through half-round rollers. I and a few others pounded our ingots flat with a hammer on an anvil and used a variety of tools to create texture on the surface. Once we had the design we wanted, we used mandrels and hammers to create a ring shape with a joint that we soldered (or technically “brazed”) together.
All of these processes required annealing beforehand to keep the silver malleable enough to work; each process caused some work-hardening of the material and it was important to remember to anneal (with flux) to keep the metal from becoming brittle. I forgot to anneal my silver before a final step and my beautiful ring cracked! Michael was kind enough to do a rush repair job and I learned my lesson.
Michael is an excellent teacher, with a way of explaining things that is clear without being overly simple. He has decades of experience as a goldsmith and artist and a lot of experience with art conservation and conservators; he connected the world of conservation to the world of making jewelry with ease and a sense of humor. It was a lovely day.
By Julia Campbell-Such